Principles of Total Quality Management & Eight Principles of TQM.
Quality Definition in Business
Quality in business means satisfying the customers by providing excellent products and services. Researchers defined quality in many ways, but the essence of the definition is almost similar. Edward described that “quality is the ability to exceed the customer’s satisfaction by providing service and product.” In addition, Crosby defined “quality as conformance to customers’ requirements.” Moreover, Juran defined quality as being ‘fitness for use. So, quality is the standard or degree of the products or services that can differentiate them from others by measurement.
Total Quality Management (TQM)
Total Quality Management (TQM) refers to the management process that includes the commitment and dedication of every employee in the organization to maintain a high level of quality in every sector for customer gratification. The employees have to be informed about the strategy before implementing it. In the mid-1980s, total quality management (TQM) was introduced based on the Company-Wide Quality Control (CWQC) and benchmarking process. Later, many scholars, such as Juran, Deming, and Ishikawa, contributed to the practices and improved the content of Total Quality Management. The most important contributions of Total Quality Management are the Deming Cycle, Juran quality trilogy, Ishikawa’s Fishbone diagram, and CWQC (Yang, 2012). For example, Netflix practices Total Quality Management, and Netflix organization changes confirm that the authority focuses on maintaining the TQM tools.
What are the Principles of Total Quality Management?
Principles of Total Quality Management
The 8 Principles of TQM are:
- Customer Focus
- Leadership
- Involvement of People
- Processes Approach
- System Approach
- Continual Improvement
- Factual Approach to Decision-Making
- Mutual Beneficial Supplier Relationship.
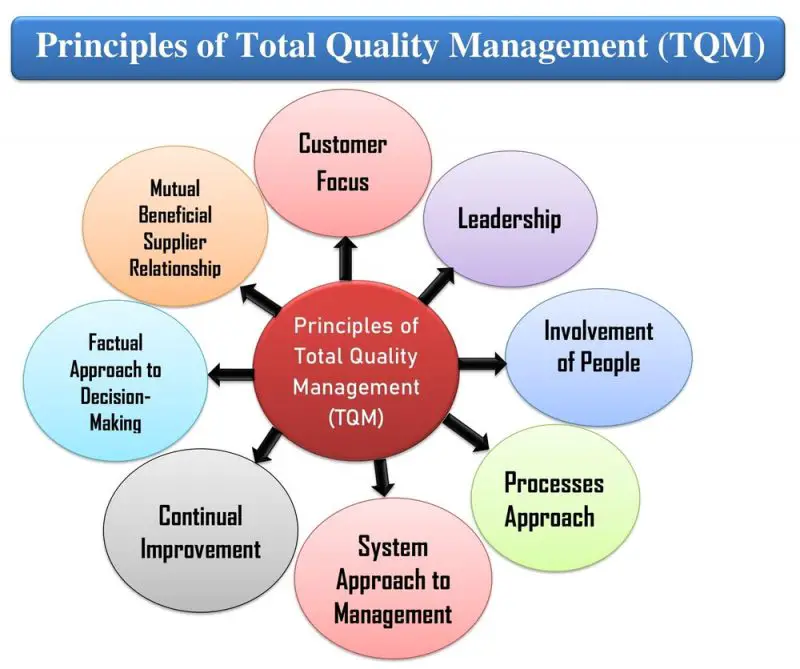
In the mid-1990s, the eight basic principles or elements of total quality management (TQM) were proposed by some well-known philosophers (Evans, 2013). These eight principles of TQM entirely work together to develop the process and yield customer satisfaction. The 8 Pillars of TQM are key components to achieve competitiveness. Many organizations adopt these TQM pillars to gain top positions in the market.
1. Customer Focus
The first and prime principle of total quality management (TQM) focuses on the existing and potential customers buying the products and services. Customers are the people who justify the quality of the products and services. So, the company needs to ensure that the customers will feel they have spent their money on a quality product if it can last long enough to fulfill demands. You can exceed customer satisfaction only when you know their needs. So, successful companies align their objectives with the client’s needs. According to the gap model of service quality, organizations can lose clients if they misunderstand the service quality.
2. Leadership
Leadership is the process by which an individual influences other people to work effectively to achieve organizational goals. They enhance relationship engagement in the organization. Leadership is essential in maintaining unity among employees to achieve interdependent goals (Evans, 2013). Although there are mainly three types of leadership in the industry, the democratic leadership style is the best to perform well. Leaders can form a convenient environment to work effectively inside the organization, where all employees work to achieve the organization’s goal. So, leadership seems to be an essential principle of total quality management.
The primary advantages of Leadership are:
The primary motive of the leaders is to motivate the employees to improve job performance.
Leaders inspire, motivate, and create a strategic plan congruent to the business goal.
They develop a precise vision for the future of the organization.
3. Involvement of People
People from every level give their all-out efforts and dedication to the organization’s profits. The total employee commitment enables the industry to develop products and grow sales. So, all the employees in the organization have to be well-trained, committed, and dedicated to achieving an interdependent goal on time. Additionally, the industry needs to create a responsive environment where every employee will be motivated to complete the task correctly. The employees’ activeness, motivation, and retention can yield customer gratification. The involvement of people can produce effective teamwork. According to Evans (2013), three types of cooperation are vertical, horizontal, and inter-organization.
The primary benefits of People Involvement are:
It influences employees who are dedicated in the workplace.
The involvement of people is an intrinsic motivation that charms employees to contribute to the organization’s growth. The process theories of motivation explain how people’s involvement and affiliation motivate employees to keep working in the workplace.
It enhances employees’ creativity and innovation in the organization.
4. Processes Approach
The company needs to improve the process consistently to yield sound output. A good result from the processes approach can bring customer satisfaction. Hence, TQM focuses on the process approach to assure product or service quality.
5. System Approach to Management
Total quality (TQM) highlights executing the strategy systematically. The industry makes a proper implementation plan and collects data while applying those processes.
The International Organization for Standardization (ISO) describes this principle: “Identifying, understanding, and managing interrelated processes as a system contributes to the organization’s effectiveness and efficiency in achieving its objectives.”
6. Continual Improvement
Continual improvement of the process is an essential step for every industry to satisfy its customers. Therefore, TQM assists the company in keeping watching the constant improvement of the system to improve the service quality and product of the industry. Above all, continual improvement assists the company in achieving competitive advantages, and it is the most critical principle among the eight principles of TQM.
7. Factual Approach to Decision-Making
An objective approach to decision-making is another crucial principle of TQM. It eases making decisions based on the information collected from data. Making a decision based on facts is an effective way to achieve customer satisfaction. This principle uses the actual method to collect and analyze data to make decisions for the company’s progress.
8. Mutual Beneficial Supplier Relationship
Mutual beneficial supplier relationship is another essential principle of total quality management for building rapport with suppliers. It is also called reciprocity. Usually, a business is conducted by multiple combined departments, and each department is assigned individual tasks, although these departments’ functions are interconnected. The total quality management process helps all sections work combined to achieve an interdependent objective. The company uses visual aids and flowcharts to understand how employees perform perfectly. Executing total quality management (TQM) is not easy; TQM represents a significant cultural shift, so the company needs to implement it slowly and accurately (Evans, 2013).
Conclusion
The Eight Core Principles of TQM are Customer Focus, Leadership, Involvement of People, Processes Approach, System Approach to Management, Continual Improvement, Factual Approach to Decision-Making, and mutually beneficial Supplier Relationship. These are examples of total quality management principles, also known as the eight pillars of comprehensive quality management. However, the eight principles of TQM are fundamental elements in driving a business successfully. Everybody in the company has to be conscious of the plan, method, and strategy to achieve a goal. The risk of failure can increase due to not maintaining the principles of total quality management. So, the authority should ensure that every employee is aware of them. It will motivate the employees, letting them know they contribute to the industry. Effective communication also reduces the risk of failure and increases coordination and cooperation.
Examples of Total Quality Management (TQM) in Practice:
- Toyota Production System (TPS): Toyota’s renowned production system is a prime example of TQM in action. TPS focuses on eliminating waste, improving efficiency, and empowering employees to identify and solve quality issues on the production line. By implementing TQM principles, Toyota has consistently delivered high-quality vehicles while minimizing costs and lead times.
- Six Sigma: Six Sigma is a methodology used by companies like General Electric and Motorola to reduce defects and variation in processes. By applying statistical tools and rigorous analysis, organizations identify the root causes of problems and implement solutions to achieve near-perfect quality levels. Six Sigma emphasizes data-driven decision-making and continuous improvement to drive business success.
- Kaizen: Kaizen, meaning “continuous improvement” in Japanese, is a fundamental aspect of TQM. Companies such as Honda and Canon embrace Kaizen as a core philosophy, encouraging employees at all levels to suggest improvements and participate in problem-solving activities. Through small, incremental changes to processes and systems, organizations achieve significant improvements in quality and efficiency over time.
-
ISO 9000 Quality Management System:
Many organizations adopt the ISO 9000 series of standards to implement TQM principles and ensure consistent quality in products and services. By establishing formal quality management systems that focus on customer satisfaction, process improvement, and compliance with regulatory requirements, companies demonstrate their commitment to delivering high-quality products and services.
- Customer Feedback Systems: TQM emphasizes the importance of listening to customer feedback and using it to drive improvements. Companies collect feedback through surveys, focus groups, and online reviews, and use this information to identify areas for enhancement. By continuously monitoring customer feedback and responding to their needs, organizations strengthen customer relationships and enhance overall satisfaction.
- Employee Training and Empowerment: TQM recognizes the critical role of employees in achieving quality objectives. Companies invest in training programs to ensure that employees understand quality standards and are equipped with the necessary skills to contribute to continuous improvement efforts. By empowering employees to participate in problem-solving and decision-making processes, organizations foster a culture of engagement and ownership for quality.
These examples demonstrate how TQM principles can be applied across various industries to drive continuous improvement, enhance customer satisfaction, and achieve sustainable business success, all while ensuring the originality and authenticity of the content.
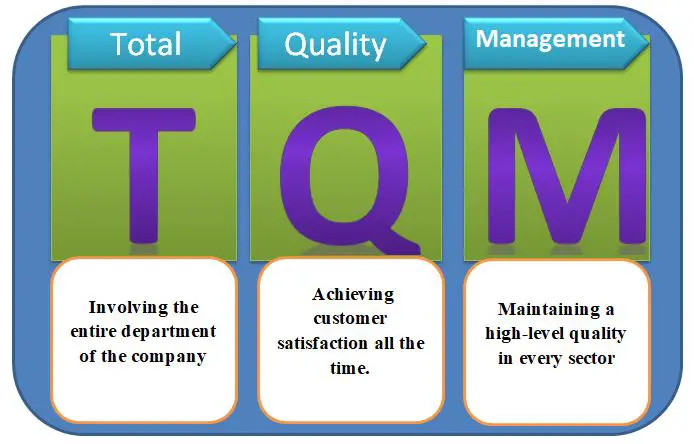
The Advantages of Total Quality Management Principles
Although Japan identified total quality management (TQM) advantages in the mid-1950s, now the benefit of the TQM is disclosed worldwide. The most important benefits of the TQM are:
The TQM principles develop the quality of products and services to satisfy customers; it motivates employees naturally and boosts their productivity.
Additionally, the principles of TQM reduce production costs and faults and make processes more efficient and reliable.
Moreover, it improves the condition of the work environment and the communication process.
Finally, the core principles of TQM raise the profit margin.
Total Quality Management Tools
The researchers introduced many tools of the TQM that help the industry operate smoothly with profit. These tools can help the industry in many approaches. For example, the fundamental strategies are; identifying difficulties with quality, analyzing data, collecting information, identifying the leading causes of the problems, and assessing the results.
Quality Strategy to Profitability in the Organization
Since the 1980s, researchers have represented diverse quality management systems to maintain the quality of the products and services in the organization, such as total quality management system (TQM), Six Sigma, reengineering, skeletal system, and so on. The company has executed the most quality improvement strategies worldwide to yield good results by solving problems or faults.
The History and Evolution of Quality Management Strategies
- Inspection quality control (IQC), since 1910
- Statistical process control (SPC), since 1930
- Total quality control (TQC), since 1950
- Company-wide quality control (CWQC), since 1970
- Total Quality Management (TQM), since 1985
- Six-Sigma (6σ), since 1986
- Business Excellence Model, since 2000
- The development and implementation system of the DMAIC Six Sigma program
References
Evans, J. R. (2013). Quality & performance excellence. Cengage Learning.
Yang, C. C. (2012). The integration of TQM and Six Sigma. Total Quality Management and Six Sigma, 219.
Citation for this Article (APA 7th Edition)
Kobiruzzaman, M. M. (2024). Principles of Total Quality Management & 8 Principles of TQM. Newsmoor- Best Online Learning Platform. https://newsmoor.com/total-quality-management-tqm-eight-principles-and-practices-of-tqm/ |